Gas Processing Equipment Cleaning
Trusted by the Biggest in the Business
ZymeFlow has been working in gas processing plants, including major LNG facilities, for decades and is the only provider called back time and time again to tackle the biggest, most dangerous cleaning projects in the world. Our patented chemistry, tailored application methods, and experienced team can handle any level of hydrogen sulfide, carbon dioxide, and fouling found in these facilities. We continuously amaze our clients by getting them into units faster and safer without the need for fresh air.
LNG Plant Decontamination
Every LNG Processing Plant has a different set of challenges, from few steam injection points to limited wastewater treatment systems. The ZymeFlow Team works directly with the customer ahead of time and on-site to address each unique concern and challenge that the plant presents. Our ZymeFlow LNG chemistry is easily able to remove LELs, hydrogen sulfide and polyphoric iron sulfides all without making a substantial impact on wastewater systems. Our tailored chemistries and processes allow you to get into units faster and safer.
Units We Service:
ZymeFlow chemistries and applications are well suited to clean virtually all components of gas processing plants. The technology has been successfully applied from upstream to midstream gas processing including separator vessels and slugcatchers, amine units, glycol or molecular sieve dehydration units, sulfur recovery units, compressor equipment, fractionation columns, and pipelines.
Slugcatchers
Separator vessels and finger-style slugcatchers used to remove liquids and solids from the raw gas often contain pyrophoric iron sulfides, dithiazine solids from oilfield treatment chemicals, and residual hydrogen sulfide. This type of equipment is often very large in volume which can extend up to a few hundred meters in length making conventional decontamination very challenging. Our chemistry is recognized as the best practice for neutralization and removal of these contaminants. For years, the largest gas fields in the world have relied on ZymeFlow for decontamination of their slugcatchers, achieving significant optimization in equipment preparation.
Processing Units
Amine units used for removal of acid gases such as carbon dioxide and hydrogen sulfide are prone to fouling with pyrophoric iron sulfide and contain high concentrations of these contaminants. Vapour-Phase® treatment or liquid circulation with our specialty chemistries can alleviate these contaminants quickly and safely. Further downstream, we can also remove paraffin foulant and residual LEL found in glycol or molecular sieve dehydration units as well as neutralization of hydrogen sulfide and pyrophoric iron sulfide in sulfur recovery units such as claus units and tail gas treaters. ZymeFlow Vapour-Phase is a far superior choice to remove LEL from fractionation trains (deethanizer, depropanizer, debutanizer columns) and pipelines when compared to costly and time-consuming nitrogen purging which does not eliminate the risk of pyrophoric events.
ZymeFlow technology can provide decontamination solutions to separate units or the entire gas processing plant.
Applicable Gas Processing Units
- Separator Vessels
- Slugcatchers
- Amine
- Glycol/Molecular Sieve Dehydration
- Sulfur Recovery
- Compressors
- Fractionation
- Pipelines
Best Results Come from the Best Planning
It all starts with thorough planning. Our in-house planning team works with the customer to address the challenges of the many varied gas processing sites found globally. Our planners first develop a cleaning strategy based on the equipment scope, resources available, contaminants and other applicable details to minimize downtime while maximizing results. Our solutions are extremely effective – while also being safe and environmentally friendly.
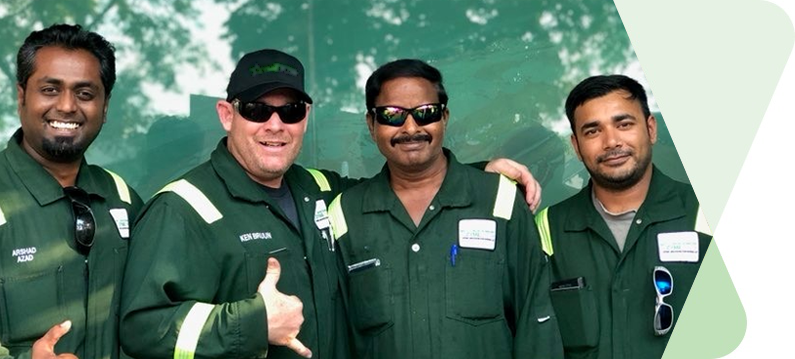
Ultra Sour Gas Plant Decontamination
One of the most sour gas plants in the world, at over 20 percent hydrogen sulfide, called on ZymeFlow for decontamination with a tight turnaround schedule. ZymeFlow not only delivered but reached 0 PPM hydrogen sulfide meaning maintenance work could be performed without fresh air - the first time in the history of the plant.
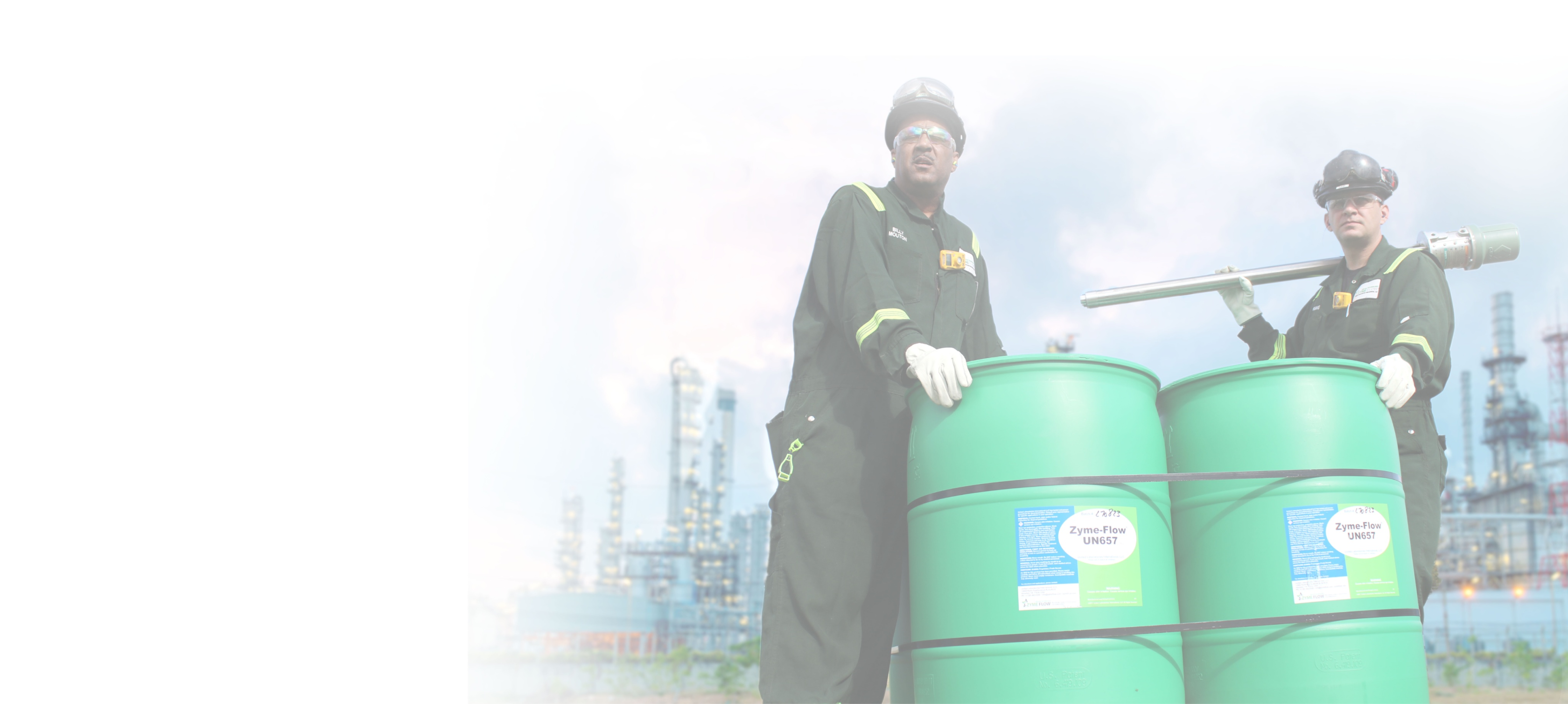